Download the Guru IA app
Android and iOS
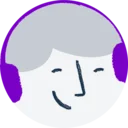
Amanda
SENT BY THE APP
3. BUILT A MIND MAP IN ENGLISH ADVANCED FORMING TECHNOLOGIES...
- BUILT A MIND MAP IN ENGLISH
ADVANCED FORMING TECHNOLOGIES
Metal-forming processes have been known for centuries. As early as 4500 BC,
copper was subjected to metal forming, originally with hammers made of durable
stones. In about 1000 BC, iron produced in the bloomeries would then be forged
c to produce steel on a large scale. Starting from the seventh century BC, in the
Greek sphere of influence, silver or electrum coins began to be made by means
of processes resembling primitive die forging. The Middle Ages witnessed a
development of forging owing to a widespread use of the water wheel, which was
used in hammer forges of the time to power hammers for open die forging. At that time, hand-operated rolling mills were also introduced, and they were used to
work easily deformable metals like lead or tin.
The earliest rolling mills powered by the water wheel were used in the
seventeenth century to produce lead sheets that were probably used to cover
bottoms of ship hulls. Hot rolling of iron and its alloys was mastered at the end of
the eighteenth century. It was then that steam-driven rolling mills were introduced
(the first such rolling mill was used in 1783 in the Wilkinson factory, England). In
the nineteenth century, an intensive development of metal-forming processes
took place, which resulted from implementing new machines and technologies,
like the steam hammer (Nasmyth, 1839), die forging (the Colt factories, 1853),
the hydraulic press (Haswell, 1861), or the continuous rolling line (Bedson, 1862).
Many new metal-forming processes were patented and implemented in the years
that followed. One of these processes was cross-wedge rolling (CWR).
The origins of CWR date back to 1879, as it was then that this forming technology
was first granted a patent in Germany. Six years later, the first attempt at
industrial application of the CWR method was made to produce stepped shafts
used in automobiles of that time. Given that the method requires high
technological capabilities, its factual development came later. It is agreed that the
first fully industrial application of CWR took place in 1949, when, at the Gorky
Automobile Plant in Russia, the method was implemented to form
connecting rods. A significant development of CWR methods took place in the
second half of the twentieth century. In those years, new rolling mills were
developed and industrially implemented, and a great deal of theoretical and
experimental research was conducted to better understand CWR process
regularities.
ADDITIVE MANUFACTURE OF TOOLS AND DIES FOR METALS FORMING
In metal forming processes, additive manufacturing technologies are mostly used
to manufacture dies for traditional forming processes, and not for the direct mass
production of parts, since additive manufacturing processes to date are often not
as fast and thereby time- and cost-efficient compared with conventional
manufacturing processes (machining, casting, forming). Furthermore, additive
manufacturing processes are not yet as accurate as desired regarding surface quality, which means that producing a net-shape is often not possible. For that
reason, in metal forming processes, additive manufacturing technologies are
mostly used to manufacture dies with high geometric complexity with, for
example, inner channels for a functional integration, which leads to an additional
benefit for the whole process or dies that cannot be manufactured by
conventional subtractive methods because of production-related restrictions.
Nevertheless, minor surface finishing often must be applied locally using
subtractive methods. According to the condition or shape of the base material
and the manner of its deposition, additively manufactured dies for metal forming
applications are presented in this chapter, grouped into layer-laminated tools, the
powder bed, and the powder nozzle–based tools.
- BUILT A MIND MAP IN ENGLISH ADVANCED FORMING TECHNOLOGIES Metal-forming processes have been known for centuries. As early as 4500 BC, copper was subjected to metal forming, originally with hammers made of durable stones. In about 1000 BC, iron produced in the bloomeries would then be forged c to produce steel on a large scale. Starting from the seventh century BC, in the Greek sphere of influence, silver or electrum coins began to be made by means of processes resembling primitive die forging. The Middle Ages witnessed a development of forging owing to a widespread use of the water wheel, which was used in hammer forges of the time to power hammers for open die forging. At that time, hand-operated rolling mills were also introduced, and they were used to work easily deformable metals like lead or tin. The earliest rolling mills powered by the water wheel were used in the seventeenth century to produce lead sheets that were probably used to cover bottoms of ship hulls. Hot rolling of iron and its alloys was mastered at the end of the eighteenth century. It was then that steam-driven rolling mills were introduced (the first such rolling mill was used in 1783 in the Wilkinson factory, England). In the nineteenth century, an intensive development of metal-forming processes took place, which resulted from implementing new machines and technologies, like the steam hammer (Nasmyth, 1839), die forging (the Colt factories, 1853), the hydraulic press (Haswell, 1861), or the continuous rolling line (Bedson, 1862). Many new metal-forming processes were patented and implemented in the years that followed. One of these processes was cross-wedge rolling (CWR). The origins of CWR date back to 1879, as it was then that this forming technology was first granted a patent in Germany. Six years later, the first attempt at industrial application of the CWR method was made to produce stepped shafts used in automobiles of that time. Given that the method requires high technological capabilities, its factual development came later. It is agreed that the first fully industrial application of CWR took place in 1949, when, at the Gorky Automobile Plant in Russia, the method was implemented to form connecting rods. A significant development of CWR methods took place in the second half of the twentieth century. In those years, new rolling mills were developed and industrially implemented, and a great deal of theoretical and experimental research was conducted to better understand CWR process regularities. ADDITIVE MANUFACTURE OF TOOLS AND DIES FOR METALS FORMING In metal forming processes, additive manufacturing technologies are mostly used to manufacture dies for traditional forming processes, and not for the direct mass production of parts, since additive manufacturing processes to date are often not as fast and thereby time- and cost-efficient compared with conventional manufacturing processes (machining, casting, forming). Furthermore, additive manufacturing processes are not yet as accurate as desired regarding surface quality, which means that producing a net-shape is often not possible. For that reason, in metal forming processes, additive manufacturing technologies are mostly used to manufacture dies with high geometric complexity with, for example, inner channels for a functional integration, which leads to an additional benefit for the whole process or dies that cannot be manufactured by conventional subtractive methods because of production-related restrictions. Nevertheless, minor surface finishing often must be applied locally using subtractive methods. According to the condition or shape of the base material and the manner of its deposition, additively manufactured dies for metal forming applications are presented in this chapter, grouped into layer-laminated tools, the powder bed, and the powder nozzle–based tools.